Horning Students See How their Ideas Have Helped Manufacturing Firm
Posted on: February 6, 2019
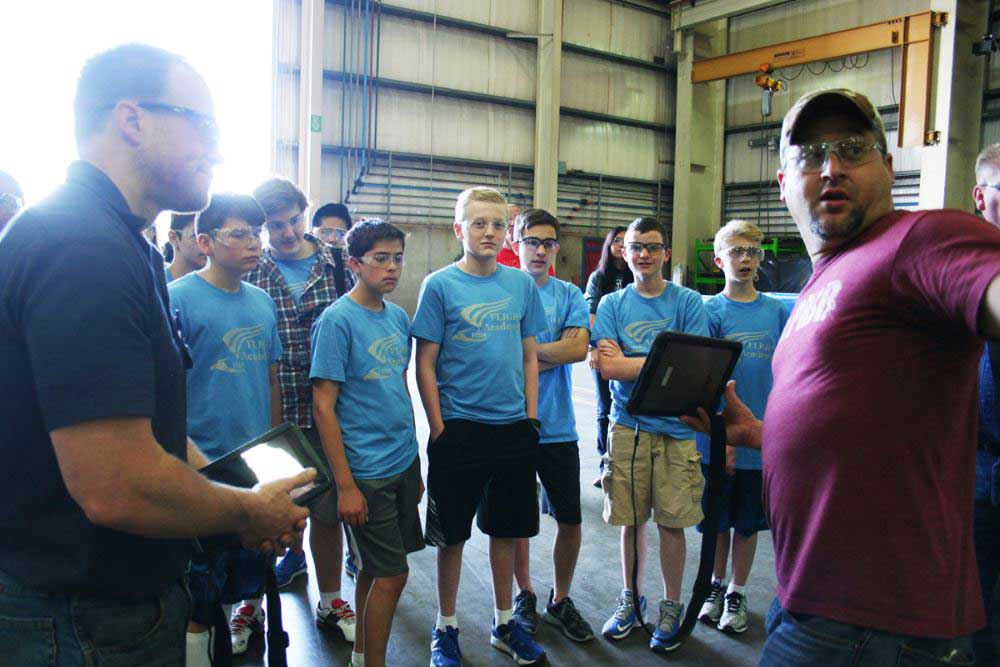
Stephan Rice, quality insurance inspector, shows off how Weldall employees use iPads to a group of Horning Middle School students Friday. Lauren Anderson/Freeman Staff.
A lot has changed in the last two years at Weldall Manufacturing, thanks to the ideas of some middle-school consultants.
In 2013, students in Horning Middle School’s FLIGHT Academy — a multi-age personalized learning program—toured Weldall to learn about the company’s operations. They returned to school and brainstormed ideas for how the company could incorporate iPads into the plant’s daily operations.
The digital natives then presented their ideas to company representatives. Among them were using Facetime to communicate on the shop floor, using Time Station to clock in and out of jobs, taking photos of their work, taking notes electronically and cutting back on paper usage.
On Friday, those students were invited back to Weldall — this time to see the fruits of their labor. Students toured the facility with company representatives who pointed out areas at nearly every turn where iPads have helped increase efficiency and communication in their day-to-day operations.
Mike Shoen, Weldall operations manager, said the company has been using the tablets for about a year and the students’ ideas inspired their use.
In some cases, the efficiency and cost savings are very tangible. Before iPads, Shoen said, supervisors and managers used to print 200-plus pages of reports that detailed each project and its status every week. Now, they use their tablets, saving hundreds of dollars per year on paper costs.
All of the tablets are connected to employees’ desktops, allowing them to access email while out on the floor. Employees often use the tablets to take photos when there is an issue, which proves particularly useful when communicating with Weldall’s plant in Slinger and with customers.
“We can take a photo from our iPad and send it to each other or to a customer,” he said. “If a customer requires any kind of documentation, we can pull up inspection reports, blueprints, anything we have here, we can pull it up on the screen and take a screenshot and send it while they’re on the phone. So it’s live communication with our customers as well.”
The list of ways in which the iPads have proved useful is long. Many employees use the Notes app to jot down information about their projects — a feature Brian Cramer, quality inspector, estimates has saved him about 30 minutes every day.
“It gives us way more time,” supervisor Ken Lee said. “We can do in minutes what used to take hours.”
An app called eDrawings allows employees to view and browse product designs. Employees can use their iPads for making vacation requests. Google Translate has helped in several cases when workers needed to interpret foreign texts. The Weather Channel app notifies employees of tornado or thunderstorm warnings — a scenario that actually happened last fall, Shoen said.
All of those efficiencies, Cramer said, are good news for the company’s bottom line.
“Time is money for us,” Cramer said. “So the faster we get things done, the more money we make.”
‘You’ve Made a Difference’
Both Waukesha School District and Weldall representatives stressed the special nature of the project that had middleschoolers helping a company improve its operations. School Board member Bill Baumgart called it “one of most unique partnerships” he’s ever seen.
“There are partnerships where students go see a plant or a company,” he said. “But this is one of the very few I remember where you took that back and did something with it and then the company listened to you, got ideas from you and put them into play.”
Shoen applauded their work.
“And you’ll continue to make a difference by doing what you do. And keep those ideas passed on so that other people can get the benefits like we have.”